I INTRODUCTION AND M OTIVATION
1.1Introduction:
This report introduces an automated indoor plant monitoring system utilizing multiple microcontrollers. The system monitors
temperature, humidity, and soil moisture, and actuates water pumps, humidifiers, and exhaust fans based on sensor readings.
A master-slave architecture with a Texas Instruments (TI) TIVA microcontroller and an ESP32 is employed. The Master Tiva
receives data via CAN bus from the Slave ESP32 dedicated to sensing and actuation. This ESP32 microcontroller with built-in
Wi-Fi enables remote communication.
Figure 1: Setup
1.2
Motivation:
Maintaining healthy indoor plants can be challenging due to one’s busy day to day schedule. Traditional methods often rely on
manual monitoring and intervention, which can be time-consuming and lead to over or under-watering, improper humidity levels,
or unsuitable temperatures. This can result in stunted growth, disease, or even plant death. This system addresses the limitations
of manual plant care by providing real-time data, automating environmental control and facilitating remote monitoring.By au-
tomating plant care and providing real-time data, this system aims to simplify the process, improve plant health outcomes, and
enhance the overall indoor gardening experience.
II BACKGROUND S TUDY
This project draws upon a variety of microcontrollers, communication protocols, sensors, and actuators to achieve automated
plant monitoring and management. TI Tiva TM4C123GH6PM serves as the core processing unit within the system. Its capa-
bilities include timers for control purposes, and general-purpose I/O pins for communication and actuation. ESP32 has built-in
Wi-Fi connectivity, enabling remote communication with the system. CAN (Controller Area Network), a high-speed and reliable
protocol facilitates communication between the master Tiva and slave ESP32. It enables efficient data exchange for sensor read-
ings and control commands. Also learnt about sensors like FC-28: Soil moisture sensor, DHT 11: Temperature and Humidity
Sensor and other components like 5V DC Relay, Ultrasonic Humidifier, Grow lights, Exhaust Fan.
III INNOVATIVE F EATURES A ND D ESIGN GOALS
1. Real-time Sensor Data Acquisition:The system continuously monitors key environmental parameters including soil mois-
ture, temperature, and humidity. This data acquisition occurs at regular intervals to provide a real-time picture of the plant’s
environment.
2. Remote Monitoring and Control via IoT Application:The system integrates with the help of Blynk Console. This ap-
plication facilitates remote access to sensor data, allowing users to monitor plants from any location. Additionally, the
application empowers users to remotely control aspects of the system, such as triggering irrigation cycles or adjusting light
schedules.
3. Automated Watering based on Sensor Feedback:The system employs a sensor-driven approach to irrigation. By analyz-
ing real-time soil moisture data, the system autonomously triggers watering cycles when necessary, ensuring optimal water
delivery and preventing overwatering.
4. Scheduled Light Cycle Management:To mimic natural light patterns, the system implements pre-programmed light sched-
ules ensuring consistent and appropriate light exposure for plant growth.
5. Automated Environmental Regulation:The system maintains ideal temperature and humidity ranges for the plant’s spe-
cific needs. By utilizing an ultrasonic humidifier and exhaust fan, the system can automatically adjust these environmental
factors to create and sustain an optimal growing environment.
6. Scalabity:The system provides scalability for multi-plant monitoring. A master Tiva communicates with multiple slave
ESP32s via CAN bus. Each slave ESP32 manages sensors and actuators for a dedicated plant zone. This distributed
architecture allows adding more slave ESP32s to the network, expanding monitoring coverage to a larger number of plants
or a wider area. This scalability offers flexibility, adapting to various indoor gardening needs.
This focus on precise data acquisition, automation, and remote control elevates the system beyond traditional plant moni-
toring solutions, fostering a data-driven and efficient approach to indoor plant care.
IV FUTURE SCOPE
1. Camera Integration:Incorporation of a camera module could enable image recognition algorithms for real-time plant
species identification and disease/pest detection. Early identification allows for timely intervention and treatment, ensuring
plant health.
2. LCD Display Implementation:Adding an LCD display would provide real-time data visualization directly on the system.
Users could view sensor readings, ongoing processes, and potential alerts without relying solely on the mobile application.
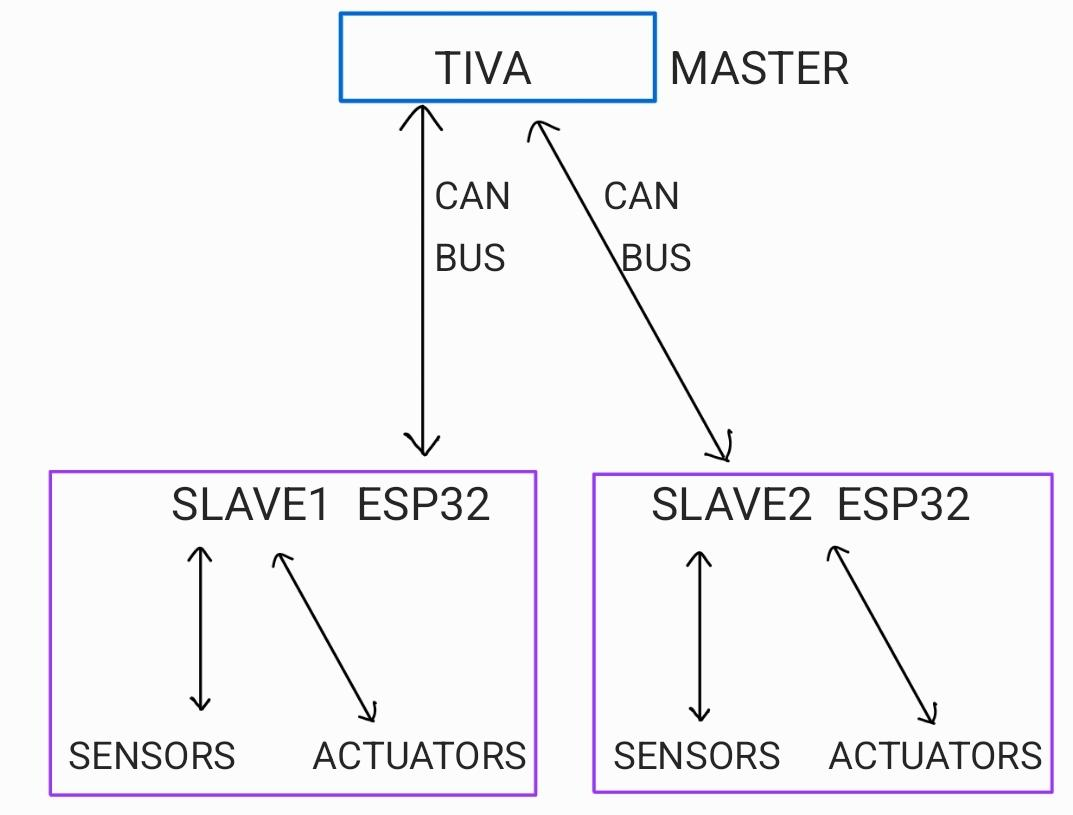
Figure 2: Block Diagram
3. Interchangeable Plant Support:The system could be designed to accommodate interchangeable plant holders or modules.
Upon introducing a new plant, the system could leverage the camera or an RFID tag to identify the plant species. This
information could then be used to automatically adjust pre-programmed settings (watering schedules, light cycles, etc.) to
match the specific needs of the identified plant.
4. Nutrient Level Monitoring and Delivery: Integration of sensors like Electrical Conductivity (EC) Sensors, Ion-Selective
Electrodes (ISEs), Optical Sensors etc, to measure nutrient levels in the soil could be explored. This data could be used to
trigger automated delivery of pre-mixed nutrient solutions, ensuring optimal plant growth.
These future enhancements hold the potential to transform the system into a truly intelligent and adaptive plant care solution,
offering a more comprehensive and user-friendly experience for indoor gardening enthusiasts.
REFERENCES
[1] Texas Instruments. (n.d.). Tiva TM4C123GH6PM microcontroller. [This is the official product page for the Tiva
TM4C123GH6PM microcontroller]
[2] Espressif Systems. (n.d.). ESP32. [This is the official product page for the ESP32 microcontroller]
[3] Can in Automation (CAN). (n.d.). [This is a website resource that provides information about the Controller Area Network
(CAN) protocol]
[4] Texas Instruments. (n.d.). Universal Asynchronous Receiver Transmitter (UART). [This is a webpage from Texas Instru-
ments that explains the Universal Asynchronous Receiver Transmitter (UART) protocol]
[5] Al-Ghobari, M., Suleiman, M., Yahya, B. E. (2020). Smart plant monitoring system using Blynk application. Interna-
tional Journal of Recent Engineering Research and Development (IJRERD), 8(7), 122-128. [This reference discusses a plant
monitoring system using Blynk application for remote monitoring]
[6] Vijiaykumar, R., Selvarani, S. (2017). Plant Monitoring System Using IOT. International Journal of Engineering Research
Technology (IJERT), 6(3), 1027-1032. [This reference explores an IoT-based plant monitoring system]
code:indoor plant system
video: Automatic Indoor Plant Monitoring System
Recent Comments